Summary
What’s the aim of running a business?
To make profits.
And how do you make profits?
By selling whatever goods and services your business creates or distributes for more than it costs you to produce or buy them.
In order to sell your products higher than it cost you to buy or produce them, you need to know the cost of goods sold formula and learn how to calculate cost of goods sold. Knowing your cost of goods sold will help you figure out how much you need to sell them at to make a profit, and if you need to reduce costs to acompete with other businesses.
What is Cost Of Goods Sold (COGS)?
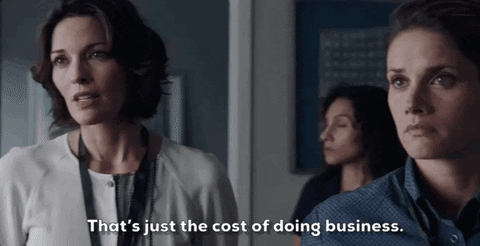
Cost of goods measures how much it costs a company to create a sellable product from scratch. For retail businesses (ecommerce, etc.) that mainly resell finished products, the cost of goods sold also refers to the costs a retailer incurs for buying and reselling a product.
Note the word sellable: COGS measures all the expenses that go into creating a product or service and getting it into the hands of paying customers.
COGS answers the question: excluding indirect expenses like marketing, sales, support, and everything else that helps us sell our products (after we’ve produced them), what does it cost us to make a finished, sellable version of this product?
What is included in the cost of goods sold & what is not?
Your COGS is made up of the direct expenses incurred in the process of buying or creating ready-to-sell products.
This includes:
- raw materials
- salaries for employees directly involved in the production, assembly, and packaging of your products
- employee benefits, such as healthcare, dental, pensions, etc.
- payroll taxes
- inventory purchase (for retail businesses)
- storage and warehousing
- utilities, i.e. rent, heating, electricity, water supply to your factories, etc.
Indirect expenses are excluded when you’re calculating your cost of goods sold. These include any other expenses that a company makes after the immediate act of creating the product, such as:
- advertising
- marketing
- salaries for your HR team
- customer service
- shipping and product delivery costs
- packaging
- endorsements, etc.
How to calculate cost of goods sold
Here's how to calculate your cost of goods sold:
- Sum your starting inventory and any supplies you bought in addition
- Subtract your ending inventory volume from the sum of both figures
The cost of goods sold formula can be expressed like this:
- Cost of goods sold = (Starting inventory + additional inventory purchases) - ending inventory
Cost of goods sold formula is restricted to a fixed period of time where you use all the variables (starting and ending inventory, additional purchases) for that period of time to calculate your COGS.
Understanding inventory cost methods and how they impact the cost of goods sold
One of the reasons why growing businesses need to know what is their cost of goods sold is that it helps them figure out their profits on the goods they’ve sold, and the cash value of the inventory they still have at hand.
Here are five different methods for calculating the value of unsold inventory to help gauge your business’s financial health.
The retail inventory method
If all your products have a fixed profit margin, add up the value of your unsold inventory, and subtract your markup (profit margin) from it.
Special identification method
The specific identification method is quite straightforward and it works by summing up your inventory costs when you stock them and subtracting any products sold to get the value of the unsold inventory.
First In, First Out Method (FIFO)
The First In, First Out method calculates the cost of goods sold based on the idea that goods produced or purchased first will as well be disposed of first.
As a result, when calculating the value of unsold inventory, you use the price of those goods bought recently since the assumption is that they'll be stored longer while those goods purchased first will be sold off quicker.
Last In First Out Method (LIFO)
The Last In, First Out method is another tactic for valuing inventory at hand based on the assumption that the most recently produced or purchased inventory will be sold first. The LIFO method is used for calculating the cost of goods sold (COGS) in a situation where the costs of producing finished products or buying inventory have been on the increase.
Weighted-average cost method
The WAC method for valuing inventory is calculated by dividing the cost of all the goods available for sale by the number of stock at hand.
The weighted average cost method works best when there’s a lump amount of inventory that can’t be divided easily or when a business deals in one particular type of product that sells for one fixed price.
Interpreting COGS for your business
There are many ways a business can use the cost of goods sold to measure the health of the business and calculate other important data points, as shown below.
Compare the prices of different products
Calculating the cost of goods sold for the different products your business sells will help you figure out which ones cost more to stock up on. With that information at hand, you can buy less of a particular product, and focus on selling goods that cost less to produce or buy at wholesale.
Figure out when to buy inventory cheaper
Calculating your COGS for particular months or weeks will show you when inventory and production costs tend to get costlier. That information will help you buy the goods and supplies when prices are lower so that you can make higher profits.
Figure out which products to sell or not sell
If your COGS shows that a product persistently costs higher than others to produce but it does not sell as quickly, you can use that data to decide to stop selling it entirely.
Calculate your gross margins
Your gross margins is the percentage of your sales revenue that you retain as profit after paying you COGS expenses — it’s a figure that you can only calculate if you know your COGS. The formula for gross margin is:
- Gross margin = (Sales Revenue – COGS) / Sales Revenue x 100
Your gross margins can help you figure out whether to increase or reduce prices, and whether to work on reducing your COGS.
Calculate your COGS ratio
COGS ratio is the fraction of your sales revenue that was spent on producing sellable versions of your product, buying inventory, etc. The formula for Cost Of Goods Sold (COGS) ratio is as follows:
- COGS ratio = COGS / Net Sales x 100
Your COGS ratio shows how much of the final sales price of your products is the cost of goods sold.
Why is it important to calculate the cost of goods sold?
Why do you need to know what is your cost of goods sold? It’s because it’ll help you to track your company’s financial health, set competitive prices, and track down fraud.
It helps you set the right price
In Economics 101, we learned that economic value is purely subjective and that your products are worth anything your customers are willing to pay for them. You only need to be careful that you don’t set your prices too low to make a profit or to cover your expenses.
That’s where the cost of goods sold come into play: it helps you figure out what it costs to produce your inventory so that you can add your mark-up and price your products accordingly and make your profits with little stress.
Calculating COGS helps you figure out if you’re turning a profit
COGS calculations are a simple way to discover if you’re turning a profit. It answers the question: "Are we selling our products more than it costs to produce?"
With that information, if you’re turning a decent profit by selling your products at a particular price, you can reduce your prices to bring in more sales. And if you realize you’re not charging enough money to make up for your cost of goods sold, you can mark-up your prices to cover up.
If you can figure out your cost of goods sold, you can reduce it accordingly
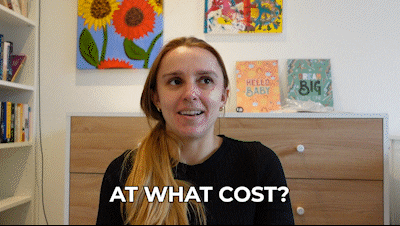
No matter what business you’re in, you can leverage economies of scale to get lower prices on your raw materials, rent, etc.
Calculating the cost of goods sold will help you figure out how much you’re spending on specific expenses which can provide an opportunity to negotiate better prices or get volume discounts by buying a little more.
Helps you track down fraud, overpaid invoices, etc.
When you subtract your expenses from your revenue, you’re left with your profits.
If you notice discrepancies, such as having less money in the bank than your profit & loss statement says you should have, it might be a sign that you’ve overpaid on invoices or that you have some fraudulent expenses going on within your company.
Effective tax management
The cost of goods sold is tax-deductible because you need to subtract how much it takes to produce your products, subtract that from your final sales price, and then pay taxes on the margin. Accurately calculating your COGS will help you figure out your profits and how much you owe in taxes to avoid overpaying on your tax bill.
Preparing for seasonal trends based on historical data
Looking at the cost of the goods you sell can help you figure out seasonal trends, i.e. when the prices of your raw materials get higher. As a result, you can stock up when they’re cheaper and sell for a bigger profit.
For instance, an ecommerce store may look at their COGS data for the past four years and realize that the shoes they buy to resell always get costlier in October - December, just before the Christmas holidays. As a result, they can stock up on more shoes during January - September, that they can sell for a bigger profit, without increasing their costs.
How to control the cost of goods sold for your business
Controlling the cost of goods sold will help you increase your profits, offer customers lower prices, and win more business.
Here are a number of tips to help you increase how much it costs to create sellable versions of your product.
Ask your suppliers for volume discounts
Depending on the volume of raw materials your business is using, you can leverage your economies of scale to ask your suppliers for volume discounts.
They may be hesitant initially, but if you communicate that you need lower prices to help your own margins and that you’re shopping around for alternatives, they’ll often come around.
This applies to small-scale businesses as well as multi-billion dollar payment processing companies like Stripe & Paypal that will reduce your payments processing fees if you reach out to sales to just ask.
For instance, let’s say you sell $1 million worth of inventory every year and you pay 3.3% on payment processing, it’ll add up to roughly $33,000 annually —that’s a lot of money left on the table. But if you can negotiate down to say, 2.2% you will pay only $22,000 and save $11,000 in processing fees.
By the time you run through your list of suppliers, you can easily knock off 10 - 20% on your cost of goods sold.
Use lower-cost materials if you can, without sacrificing quality
As the saying goes, you get what you pay for. But, do you? Does that sentiment apply in every scenario? As you’ll see, it’s not always.
If you’re willing to spend time searching for long enough, you’ll find that there are alternatives to the raw materials and suppliers that you currently use that offer the same quality for a lower price.
Automate manual, repeatable tasks
Manual tasks can take up the time required for more important work and can cost as much. Machinery and software can help you automate repetitive tasks that need little or no creative input so that you can focus on tasks that have a direct impact on your business’s revenue.
Outsource tasks to freelancers and contractors
Full-time employees can cost 30% - 60% more than freelancers and contractors and that’s before you factor in benefits, promotions, training, health insurance, office space, etc.
Thanks to remote work, you can outsource work to the world’s best freelance talent anywhere across the globe for less than it’d cost to retain full-time employees.
Identify and eliminate waste
A huge part of reducing your COGS is taking a long, hard look at each expense to see if it’s necessary and how much of it can be reduced without hurting your company’s bottom line.
Reducing waste can mean moving to a smaller office, reducing your packaging, eliminating unused utilities, etc.
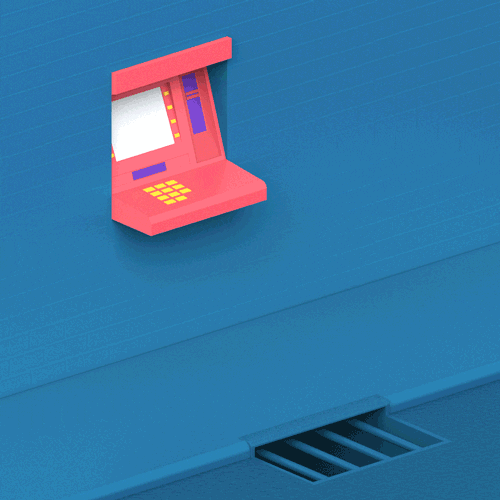
Increase your prices
Increasing your price is the simplest way to improve your business’s finances, after all, it will help you make more profits while your cost of goods sold stays the same.
Of course, you need to factor in how strong of a brand you have, and how replaceable your products and services are to ensure that even if you lose a few customers, you can end up with more money from your remaining paying customers.
Grow your margins by reducing your cost of goods sold
Running a business can get overwhelming — especially if you don’t know where the money is going and if you’re still turning a profit on your sales.
Tracking your cost of goods sold will help you figure out your major expenses, how you can reduce them, and how to increase your profit margins without reducing the quality of your products and service.